The submerged arc furnace is used for melting of silicon series, manganese
series, chrome series, nickel series ferroalloy and other ferroalloy, calcium
carbide, yellow phosphorus During work the electrodes are submerged into
material, work principle of SAF is to melt the furnace materials(granular or
powder- form) utilizing the heat of arc and resistance so to make reduction to
oxides
TECHNICAL PRIORITY
MAIN TECHNICAL PARAMETERS
Rational selection of basic parameters Power density on furnace
bottom power gradient current density of electrode voltage
gradient reactance of high current conductor system as
Well as current
density of HCCS guarantee electrodes reliably submerged into furnace material
, reach to latent melting state as well as higher productivity and lower
electric
consumption
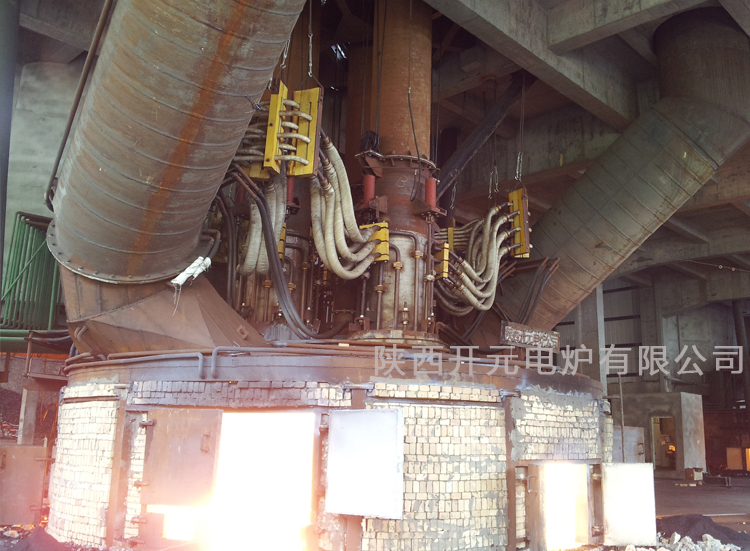
High current conductive system
Strictly adhere the
following design criterion minimum system impedance maximum active
power maximum power factor lower asymmetrical coefficient of three phase
impedances regarding to the structure of HCCS its length have to be made as
shorted as possible, and the connecting points have to be as fewer as possible,
and, the materials with higher conductivity, lower contact resistance and
identical expansion coefficient have to be used preferably so as to reduce
power loss and hot stop of work In the space surrounding the HCCS, the
magnetic metals should be minimized and all the steel structures must be earthed
well; The high current conductors have to be supported by nonmagnetic stainless
steel parts
Electric control system
This control system has the
following functions of measuring, control, protection, operation, management and
status monitoring promote the submerged arc furnace becoming large scale,
control automation, symmetry of three phase power, make the electric power and
thermal energy to be centralized at centre of furnace and enabling the main
sinking zone is located at the center of pitch circle of electrodes and so
electric consumption reduced and output raised
Insulation
Proper multi-layer insulation and
sealing no arcing and no electric leakage occurred during operation, less
failures, higher operating ratio , normal production can be guaranteed
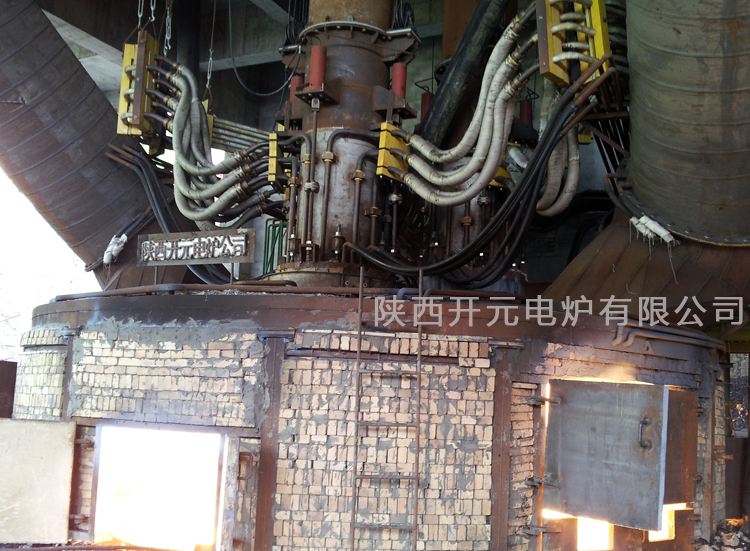
Matching equipment purchased
All the purchased
matching equipment are of the products with advanced top quality, which covers
furnace transformer high voltage power supply system hydraulic system as well
as the purchased metallic materials
Advanced manufacturing techniques
Professional
manufacturing techniques with advanced skills, based on many years experiences
with rationality , economy and reliability and requirements of design drawing to
manufacture
All the parts and components of furnace
Take responsibility for customer
Frequently occurred
failures on quality have been improved, for example, the electrode clamping
mechanism of DEMAG design and conductive copper jar are utilized with proper
conductive property , no water leakage and no magnetic induction The clamping
ring has been modified and no oil leakage occurred In the course of design and
manufacturing , the change of market status is considered in full
The
specification and data of furnace can fully meet the requirements of
customer Product quality on design, manufacturing, installation are to be
carried on conforming to international standards ISO9001 and therefore our
products have stronger competition priority